|
1.6.3.1. Выбор измерительных средств для контроля размеров
На рис. 3.3 показаны кривые распределения размеров деталей (yтех) и погрешностей измерения (yмет) с центрами, совпадающими с границами допуска. В результате наложения кривых yмет и yтех происходит искажение кривой распределения y(σтех, σмет), появляются области вероятностей m и n, обусловливающие выход размера за границу допуска на величину с. Таким образом, чем точнее технологический процесс (меньше отношение IT/Δмет), тем меньше неправильно принятых деталей по сравнению с неправильно забракованными.
Решающим фактором является допускаемая погрешность измерительного средства, что вытекает из стандартизованного определения действительного размера как и размера, получаемого в результате измерения с допустимой погрешностью.
Допускаемые погрешности измерения δизм при приемочном контроле на линейные размеры до 500 мм устанавливаются ГОСТ 8.051-81, которые составляют 35-20% от допуска на изготовление детали IT. По этому стандарту предусмотрены наибольшие допускаемые погрешности измерения, включающие погрешности от средств измерений, установочных мер, температурных деформаций, измерительного усилия, базирования детали. Допускаемая погрешность измерения δизм состоит из случайной и неучтенной систематической составляющих погрешности. При этом случайная* составляющая погрешности принимается равной 2σ и не должна превышать 0,6 от погрешности измерения δизм.
В ГОСТ 8.051-81 погрешность задана для однократного наблюдения. Случайная составляющая погрешности может быть значительно уменьшена за счет многократных наблюдений, при которых она уменьшается в √n раз, где n — число наблюдений. При этом за действительный размер принимается среднеарифметическое из серии проведенных наблюдений.
При арбитражной перепроверке деталей погрешность измерения не должна превышать 30% предела погрешности, допускаемой при приемке.
Значения допустимой погрешности измерения δизм на угловые размеры установлены по ГОСТ 8.050-73.
Рис. 3.3. Кривые распределения контролируемых параметров, построенные с учетом погрешностей измерения
Разрешается увеличение допустимой погрешности измерения, указанной в ГОСТ 8.051-81 и ГОСТ 8.050-73, при уменьшении допуска размера, учитывающего это увеличение, а также в случае разделения изделий на размерные группы для селективной сборки.
Установленные стандартом погрешности измерения являются наибольшими, которые можно допустить при измерении: они включают в себя случайные и неучтенные систематические погрешности измерении, все составляющие, зависящие от измерительных средств, установочных мер, температурных деформаций, базирования и т. д.
Случайная погрешность измерения не должна превышать 0,6 от допустимой погрешности измерения и принимается равной 2σ, где σ — значение среднего квадратического отклонения погрешности измерения.
При допусках, не соответствующих значениям, указанным в ГОСТ 8.051-81 и ГОСТ 8.050-73, допустимую погрешность выбирают по ближайшему меньшему значению допуска для соответствующего размера.
Влияние погрешностей измерения при приемочном контроле по линейным размерам оценивается параметрами:
- m — часть измеренных деталей, имеющих размеры, выходящие за предельные размеры, принята в числе годных (неправильно принятые);
- n — часть деталей, имеющих размеры, не превышающие предельных размеров, забракованы (неправильно забракованные);
- c — вероятностная предельная величина выхода размера за предельные размеры у неправильно принятых деталей.
Рис. 3.4. График для определения параметра m
Значения параметров m, n, c при распределении контролируемых размеров по нормальному закону приведены на рис. 3.4-3.6.
Сплошные линии соответствуют распределению погрешности измерения по нормальному закону, а пунктирные — по закону равной вероятности.
При неизвестном законе распределения погрешности измерения для параметров m, n, c рекомендуется принимать средние их значения, определенных по сплошной и пунктирной линиям.
Параметры m и c на графиках определены с доверительной вероятностью 0,9973.
Для определения m с другой доверительной вероятностью необходимо сместить начало координат по оси ординат.
Кривые графиков (сплошные и пунктирные) соответствуют определенному значению относительной погрешности измерения, равной
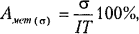
где | σ — среднее квадратическое отклонение погрешности измерения;
IT — допуск контролируемого размера.
|
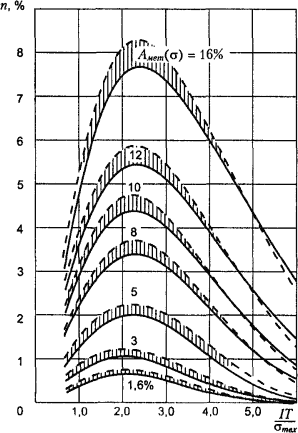 | 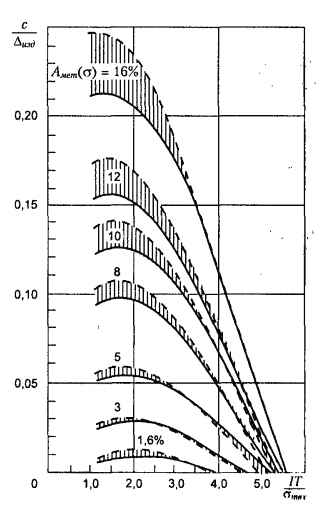 |
Рис. 3.5. График для определения параметров n |
Рис. 3.6. График для определения параметров c |
При определении параметров m, n, с рекомендуется принимать Aмет(σ) = 16% для квалитетов 2-7, Aмет(σ) = 12% — для квалитетов 8 и 9, Aмет(σ) = 10% — для квалитетов 10 и грубее.
Параметры m, n, c приведены на графиках в зависимости от значения IT/σтех, где σтех — среднее квадратическое отклонение погрешности изготовления. Параметры m, n, c даны при симметричном расположении поля допуска относительно центра группирования контролируемых деталей. Для определения m, n, c при совместном влиянии систематической и случайной погрешностей изготовления пользуются теми же графиками, но вместо значения IT/σтех принимается для одной границы (IT + 2αT)/σтех, a для другой — (IT — 2αT)/αтех, где αT — систематическая погрешность изготовления.
При определении параметров m и n для каждой границы берется половина получаемых значений.
Возможные предельные значения параметров m, n, c/IT, соответствующие экстремальным значениям кривых (на рис. 3.4-3.6), приведены в табл. 3.5,
Таблица 3.5
Aтех(σ) | m | n | c/IT | Aмет(σ) | m | n | c/IT |
1,60 |
0,37-0,39 |
0,70-0,75 |
0,01 |
10,0 |
3,10-3,50 |
4,50-,4,75 |
0,14 |
3,0 | 0,87-0,90 | 1,20-1,30 | 0,03 | 12,0 | 3,75-4,11 | 5,40-5,80 | 0,17 |
5,0 | 1,60-1,70 | 2,00-2,25 | 0,06 | 16,0 | 5,00-5,40 | 7,80-8,25 | 0,25 |
8,0 | 2,60-2,80 | 3,40-3,70 | 0,10 | | | | |
Первые значения m и n соответствуют распределению погрешностей измерения по нормальному закону, вторые — по закону равной вероятности.
Предельные значения параметров m, n c/IT учитывают влияние только случайной составляющей погрешности измерения.
ГОСТ 8.051-81 предусматривает два способа установления приемочных границ.
Первый способ. Приемочные границы устанавливают совпадающими с предельными размерами (рис. 3.7, а).
Пример. При проектировании вала диаметром 100 мм оценено, что отклонения его размеров для условий эксплуатации должны соответствовать h6(100-0,022)- В соответствии с ГОСТ 8.051-81 устанавливают, что для размера вала 100 мм и допуска IТ = 0,022 мм допускаемая погрешность измерения σизм = 0,006 мм.
В соответствии с табл. 3.5 устанавливают, что для Aтех(σ) = 16% и неизвестной точности технологического процесса m = 5,0 и c = 0,25 IT, то есть среди годных деталей может оказаться до 5,0% неправильно принятых деталей с предельными отклонениями +0,0055 и -0,0275 мм.
Если полученные данные не повлияют на эксплуатационные показатели вала, то на чертежах указывают первоначально выбранный киалитет. В противном случае назначают более точный квалитет или другое иоле допуска в этом квалитете.
Второй способ. Приемочные границы смещают внутрь относительно предельных размеров.
При введении производственного допуска могут быть два варианта в зависимости от того, известна или неизвестна точность технологического процесса.
Вариант 1. При назначении предельных размеров точность технологического процесса неизвестна. В соответствии с ГОСТ 8.051-81 предельные размеры изменяются на половину допускаемой погрешности измерения (рис. 3.7, б). Для примера, рассмотренного выше, .
Вариант 2. При назначении предельных размеров точность технологического процесса известна. В этом случае предельные размеры уменьшают на значение параметра с (рис. 3.7, в).
Предположим, что для рассмотренного выше примера IТ/σтех = 4 (при изготовлении имеется 4,5% брака по обеим границам): Aмет (σ)= 16%, c/IT — 0,1; с = 0,0022 мм.
С учетом данных диаметр вала принимают .
|